MASS FLOW FILLERS
In mass flow filling systems, Coriolis flow meters at each filling station measure the mass and volumetric flow rates of fluids with widely-differing characteristics, such as in syrups, sauces, shampoos, detergents, cleaning products, chemicals, and more. Flowmeters used in this type of system also measure the density and temperature of fluids to calculate other parameters such as volumetric flow, solids content, or density units. Each flowmeter is factory-calibrated and sized to optimize flow rates for varying fill sizes, delivering high filling accuracy (σ = 0.1%, pending product). These systems function with exceptional reproducibility, ensuring optimum fill weight, with minimal waste and product giveaway. They are also available in XP/ATEX configurations for hazardous applications, as needed.
Rotary Filling Technologies
We offer 3 specific filling technologies: Mass Flow, Net Weigh, and Volumetric. When deciding on the best filling technology for your application, consider the unique requirements of the product you are trying to fill.
*Pending Product & Fill Volume
Viscosity is not a reference characteristic because it does not completely tell us how a product will flow. For example: Corn syrup has a viscosity of approx. 4,000 cps and ketchup a viscosity of approx. 50,000 cps. From experience, ketchup will require less pressure to fill versus the corn syrup. The reason being is that ketchup is a non-Newtonian fluid meaning its viscosity is dependent on the amount of shear stress that is applied to it.
Ketchup is also shear-thinning, meaning its viscosity lowers when a shear stress is applied to it. Corn syrup is a Newtonian fluid, meaning its viscosity is constant no matter what shear stresses are applied.
There are many other factors that can affect a product’s ability to flow (i.e,. Rheology). Customer’s actual products are required to determine best results versus referencing a known viscosity to determine the ideal filling technology vs. filling head combination.
Mass Flow Filling Technology: Dispensing Valve
- Sanitary valve design incorporated with laminar flow nozzles
- Fixed-nozzle body or configurable removable tip for ultimate product flexibility
- Wire EDM bubble breaker nozzles for foaming liquids, with no loose screens
- No contact with the top of the next, eliminating risk of cross-contamination of product between container changeovers
- Optional positive nect control, based on application
Hygienic and Cleanable
Our mass flow and net weigh filling systems are designed to meet the highest level of hygienic design standards:
- Certified for 3-A SSI standard 17-13
- Active member of EHEDG (European Hygienic Engineering & Design Group).
- Designed to be cleaned or sterilized in place (without human intervention)
- Designed to clean product delivery through the filling turret and absorb turbulent flow through the product delivery line at a minimum of 5 ft/s (1.5 m/s)
- Closed-loop available for CIP/Sterilization or open tray to central collecting drain
- CIP recipes are variable per product & cleaning requirements
- Product supply pump and CIP supply are customer-supplied, with pump flow rates to match product delivery/rate requirement and CIP supply requirements
Our mass flow filling systems are available in speeds ranging from 337 to 667 CPM/2000-4000 BPH.
They are built with a sloped filler deck or traditional flat base, with filler turret sizes from 1080, 1350, 1440, 1800, 2160, 2700, or 3300 mm. Capper/Plug (monoblock) turret sizes are available from 450, 480, 540, 600, 720, 900, or 1100 mm.
Our mass flow and net weigh filling machines are available in stand-alone (filler only), monoblock (integrated filler/seamer or filler/capper), or triblock (integrated rinser/filler/capper or filler/plugger/capper) configurations.
- Mass Flow
- Mass Flow Filling
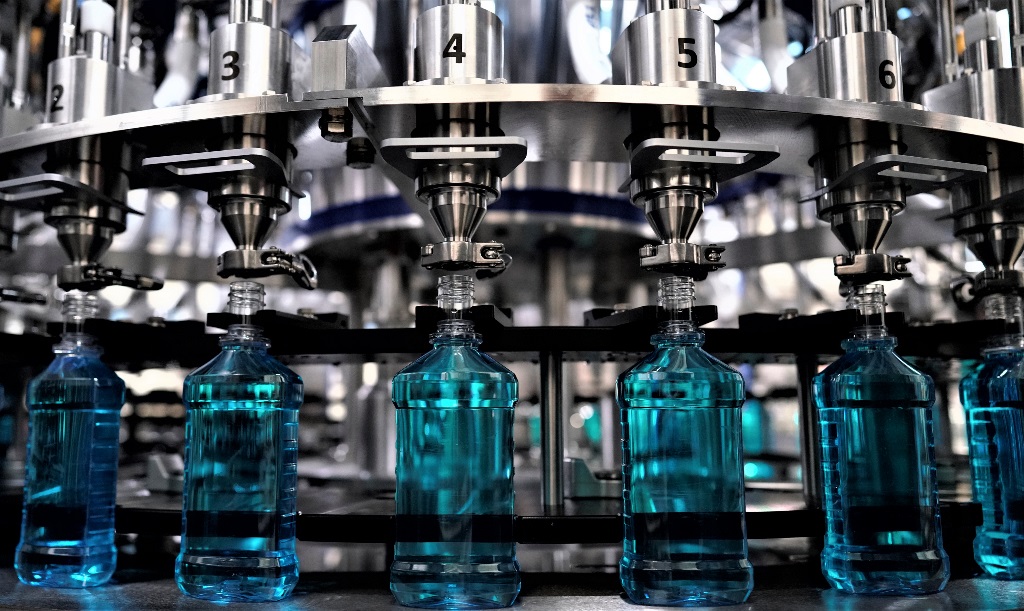